WIederaufbau und inbetriebnahme einer Abfüllanlage
Zu Beginn des Projekts wurde die bestehende Programmierung der Anlage durch unsere SPS-Spezialisten (Speicherprogrammierbare Steuerungen) analysiert und angepasst. Diese Neuprogrammierung umfasste sowohl die Optimierung der Steuerungslogik als auch die Implementierung zusätzlicher Funktionen, um den Produktionsablauf zu verbessern. Im Zuge dieser Arbeiten wurden auch neue Endlagen-Positionssensoren installiert, die eine präzisere Steuerung und Überwachung der Bewegungsprozesse ermöglichen.
Ein wesentlicher Bestandteil unserer Aufgabe war die Durchführung sicherheitstechnischer Änderungen an der Anlage, um den aktuellen Normen und Vorschriften zu entsprechen. Hierbei wurden verschiedene Komponenten im Schaltschrank ergänzt und neu verkabelt, um die Sicherheitsstandards zu erhöhen und einen reibungslosen Betrieb der Anlage zu gewährleisten. Zudem fand eine umfassende Überprüfung der gesamten Sensorik und Aktorik der Anlage statt, um sicherzustellen, dass alle Systeme ordnungsgemäß funktionierten und die geforderten Leistungsparameter erfüllten.
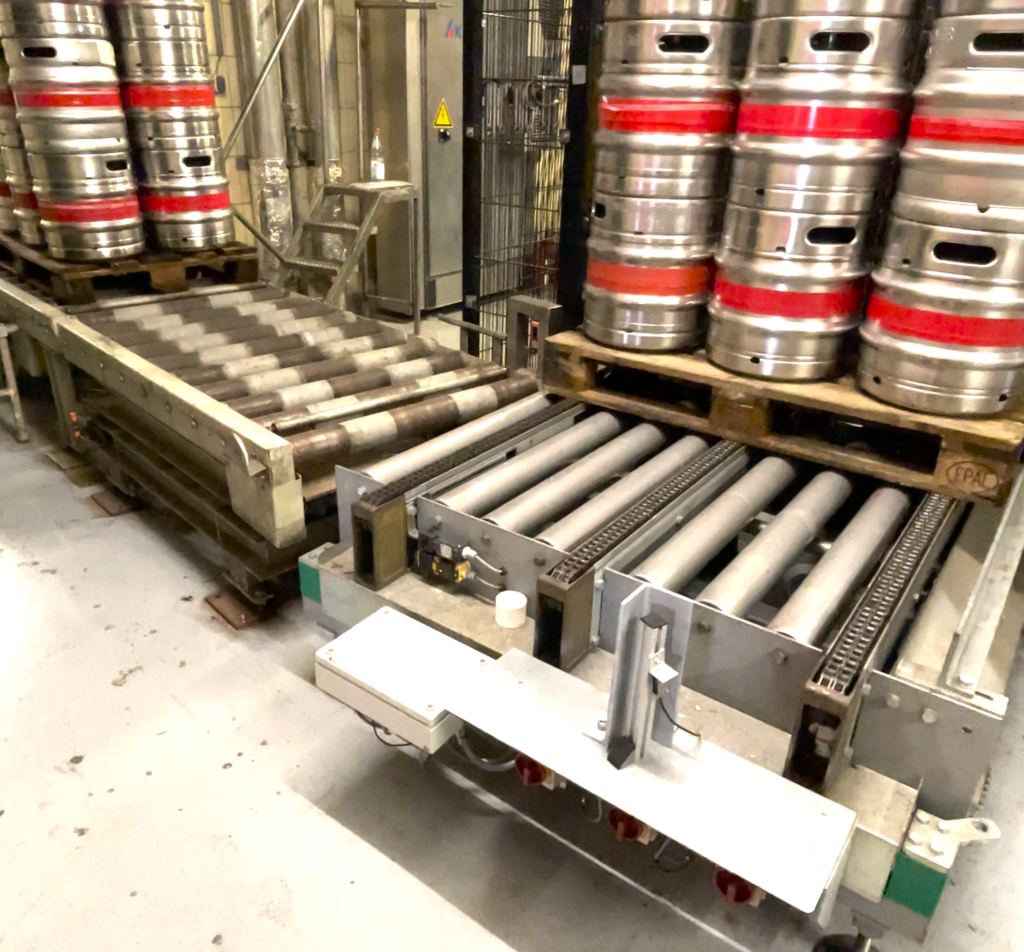
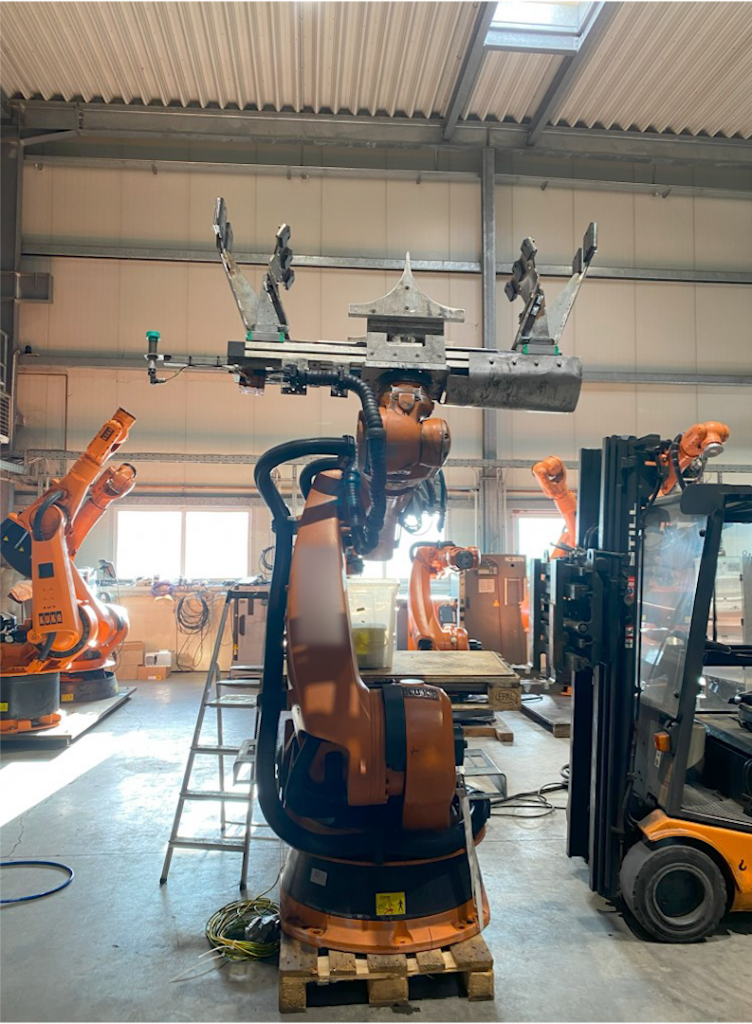
Wartung und Überprüfung des KUKA-Roboters KR 150 und des montierten Fassgreifers
Ein weiterer wichtiger Aspekt des Projekts war die Wartung des KUKA-Roboters, der mit einem speziellen Fassgreifer ausgestattet ist. In unseren Räumlichkeiten wurde der Roboter einer gründlichen Wartung unterzogen. Dabei wurden verschlissene Komponenten des Greifers erneuert, um die Funktionalität und Effizienz des Roboters sicherzustellen. Nach der Wartung wurde der Roboter an seinen neuen Platz innerhalb der Produktionslinie versetzt.
Roboter KR 150
- Ölwechsel: Optimale Schmierung der Getriebe.
- Elektrische Komponenten: Test und Kontrolle der Motoren.
- Sicherheitsprüfung: Überprüfung aller sicherheitsrelevanten Funktionen.
Fassgreifer
- Überprüfung: Sicht- und Funktionskontrolle der Linearführungen
- Verschleißteile: Austausch defekter Linearlager und verschlissener Gummiauflagen
- Pneumatik: Funktionsprüfung und Kontrolle der Luftleitungen und der Pneumatikzylinder.
- Funktionsprüfung: Test auf sicheren Griff und Fasshandling.
Die Abfüllanlage, die von unserem Team überprüft und optimiert wurde, umfasst eine Staplerstation, an der die Fässer beladen werden. Von dort aus gelangen die Fässer über Rollbahnen zum Roboter, der diese ablädt und in die Abfüllanlage setzt. Nach der Reinigung und Neubefüllung der Fässer erfolgt die Rückführung zu dem Roboter, der die Fässer entnimmt und auf Paletten stapelt. Dieser Prozess wurde so optimiert, dass die Stapelung präzise erfolgt und eine optimale Raumnutzung gewährleistet ist. Die palettierten Fässer werden anschließend über Rollbahnen wieder zu einem Entladeplatz für den Stapler transportiert.
Unsere Mitarbeiter haben einen wesentlichen Beitrag zu diesem Projekt geleistet, indem sie ihre Fachkompetenz und ihr Engagement in alle Phasen der Überprüfung und Anpassung einbrachten. Besonders hervorzuheben ist, dass dieser Prozess äußerst nachhaltig war, da wir die bestehende Anlage umfassend optimiert haben, anstatt eine neue Anlage zu installieren. Durch diese Vorgehensweise konnten wertvolle Ressourcen geschont werden.